Fancy a challenge in our BMW iFactory? Find creative solutions for real problems in the area of „lean, green & digital“ in a 24-hour-challenge and develop the first prototypes for our Innovation Hub Dingolfing together with an interdisciplinary team. Great prizes and exciting insights into the world of work at the BMW Group and our cooperation partners of the Ecosystem Ostbayern, an association of regional business and science, await you. Further, take your chance to network at various locations and maybe even find your dream job!
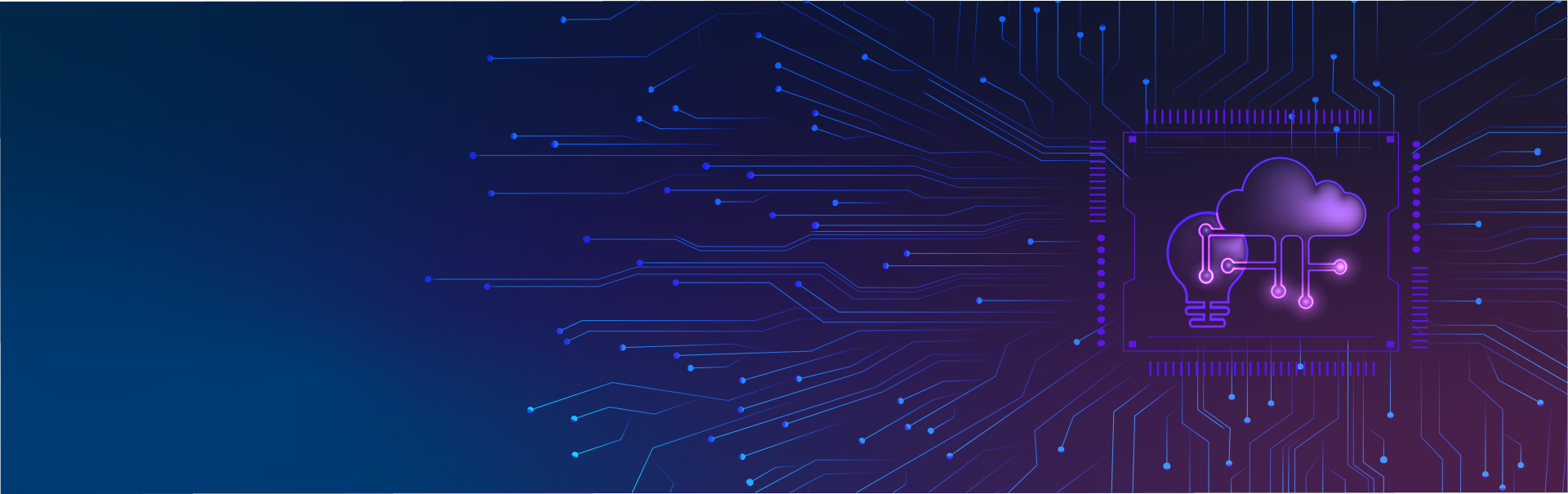
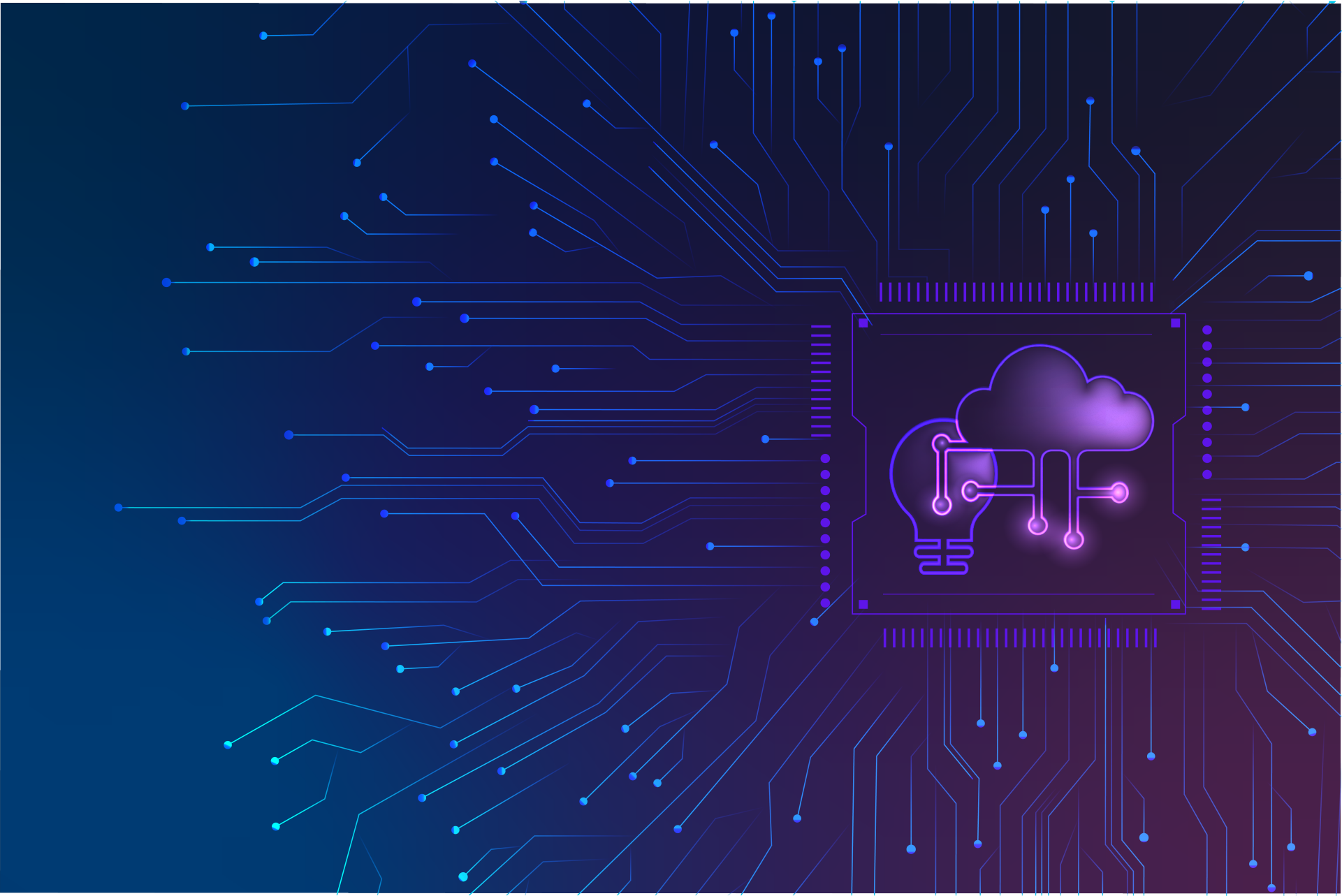
Ready for a challenge?
INNOVATION CHALLENGE FOR STUDENTS AT THE BMW GROUP PLANT DINGOLFING.
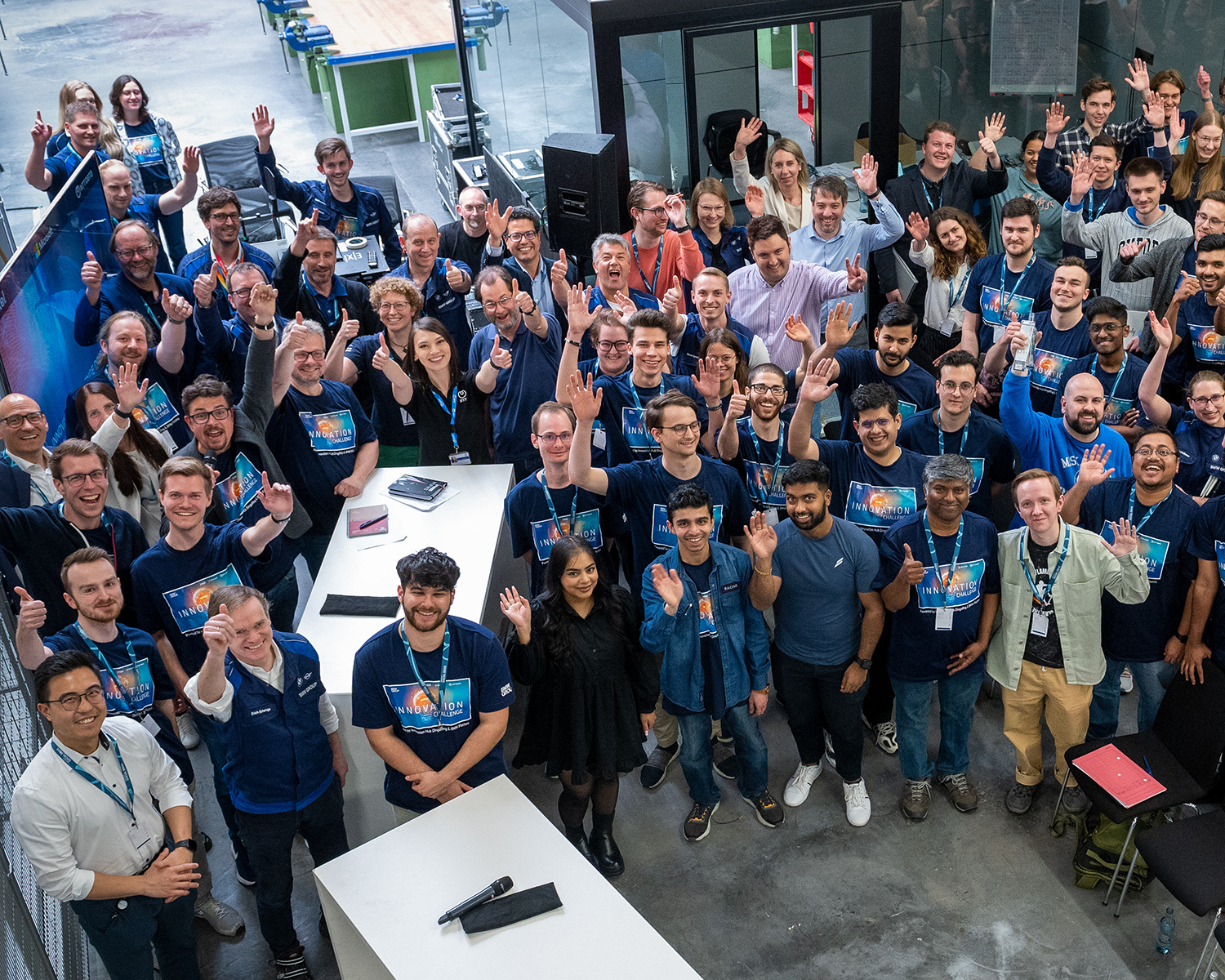
Register now!
When: Friday, 03 May to Saturday, 04 May 2024
Where: BMW Group Plant Dingolfing
- Due to limited capacity, the number of participants for the Innovation Challenge is limited. Secure your place and apply now!
- You can find the descriptions of each use case below. Take a look to see which challenge you would like to work on and what requirements you already have.
Register by 20 April 2024!
Not an IT-Nerd? No problem! Whatever you study – please apply! We are looking forward to having various perspectives on our Use Cases!
Simply complete the PDF form digitally and send it to innovationchallenge@bmw.de. You also have the possibility to attach your CV. Please register for at least 3 use cases in order to complete your registration and note that we can only consider fully completed forms including confirmation of the declarations of consent. Registration will end automatically once all places are filled.
WHAT TO EXPECT AT OUR INNOVATION CHALLENGE.
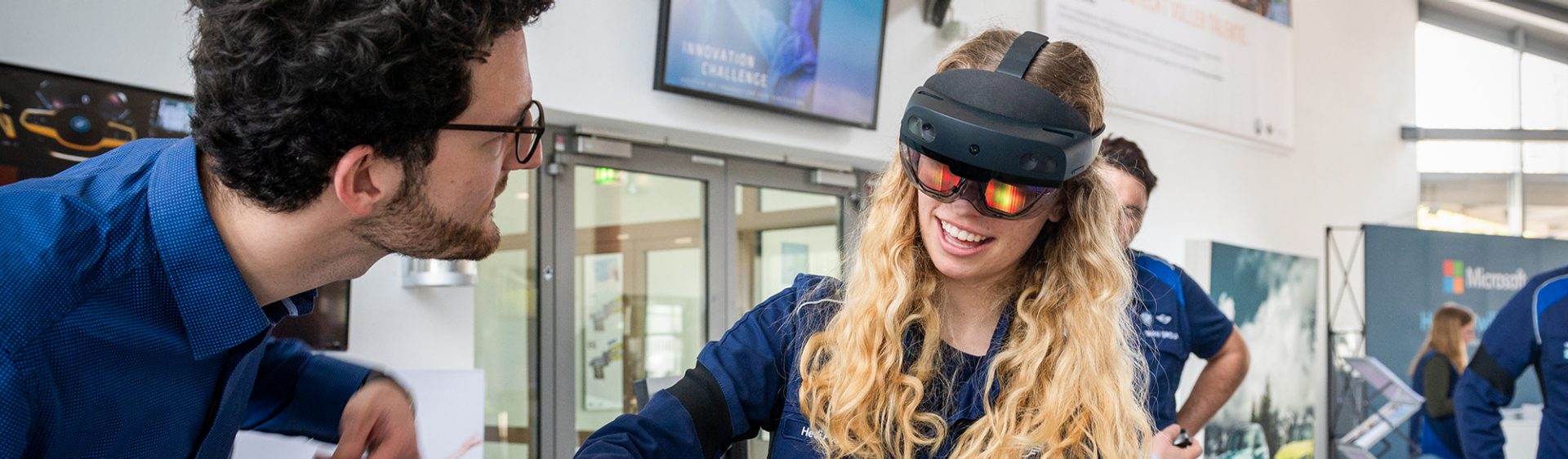
Working on Use Cases.
Working on Use Cases.
Together with an interdisciplinary team you will work on a real problem in the area of "lean, green & digital". Our colleagues from the specialist departments of the BMW Group and from our cooperation partners Intel, Microsoft and NTT are available to you and accompany your project. You have 24 hours to solve the problem of your use case and to develop your prototype.
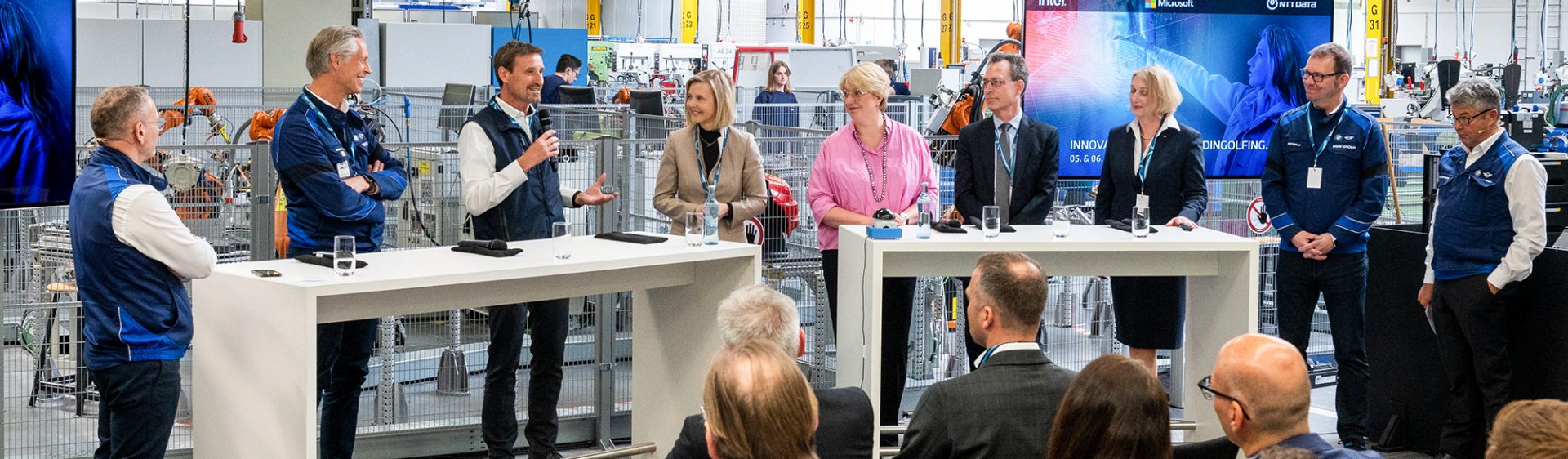
Exciting Insights & Networking.
Exciting Insights & Networking.
As you will be on site at our BMW Group plant in Dingolfing and the sites of our partners, you will gain exciting insights into our companies. Through the support of colleagues from the specialist departments of the BMW Group as well as our cooperation partners, you will get to know us personally and can make contacts that could help you later for internships or your thesis, for example.
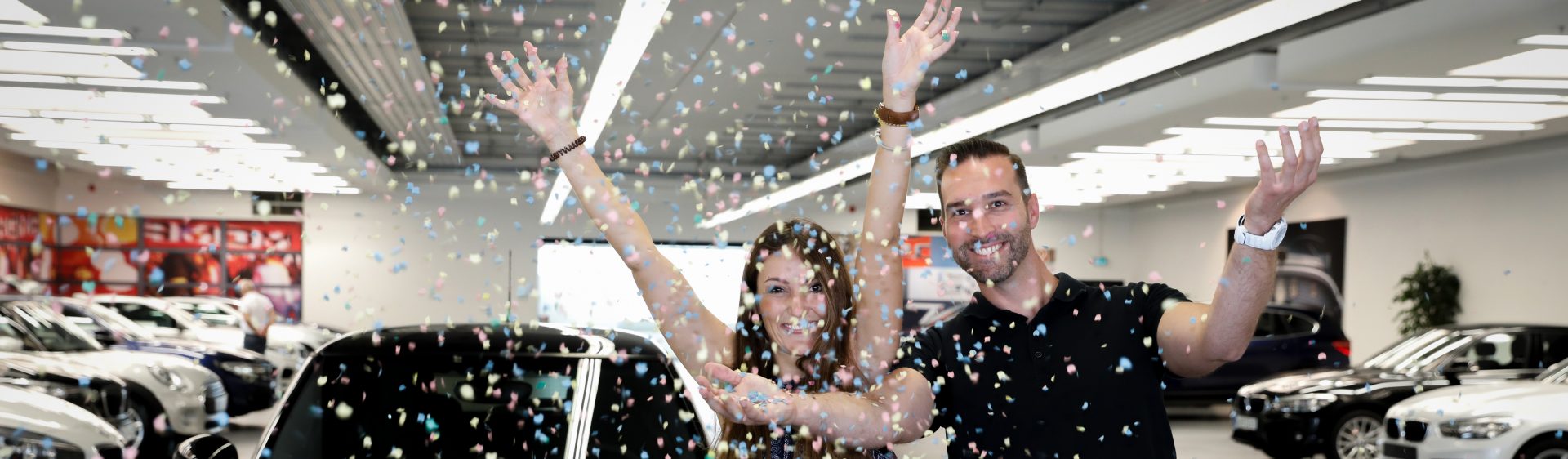
Great Prizes.
Great Prizes.
In addition to exciting insights that you can gain through the Innovation Challenge, we also award great prizes to the winners of the challenge. You will learn more about it at the event. So, stay tuned for an exciting experience!
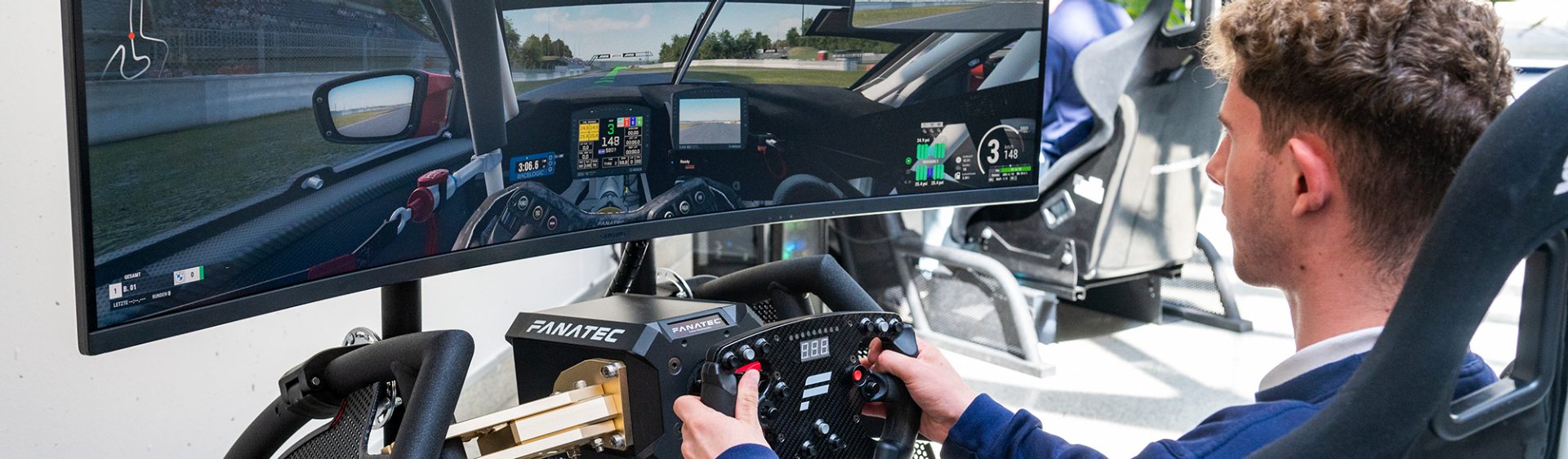
Engaging Supplementary Programme.
Engaging Supplementary Programme.
We will take care of all the sideshow! So you can fully concentrate on your challenge. We provide catering and quiet areas to relax and have a great time – we also end the success of the Innovation Challenge with a joint barbecue.
- Story 1
- Story 2
- Story 2
- Story 4
USE CASES.
Host and Location.
- This use case is hosted by SAR
- Location: SAR office
Motivation.
Our innovative systems are designed to counteract the shortage of skilled labour in the food service industry. KNEXT Futurecafés as the world's first fully integrated, autonomous, robotic coffee shop systems for premium use, have been successfully established in the German market. Due to the high demand, it is necessary to further improve the systems in order to optimise throughput.
Target.
To improve the guest experience, the parallel ordering and production processes are to be continuously improved with the help of machine learning.
Distribution of Activities.
100% fun (consisting of 30% concept creation, 60% coding, and 10% coffee enjoyment)
Useful knowledge.
- AI
- Angular
- Java / Spring Boot / (Python) / Hibernate
- Eclipse / STS
- REST Service / Json
- SQL / PostgreSQL
- OpenVINO
Host and Location.
- This use case is hosted by DE software & control GmbH
- Location: DE office
Motivation.
High-quality work instructions are essential for efficiency and safety in the modern working world. However, the quality of these instructions vary widely, depending on the skills of the staff. Our goal is to standardize and simplify this process.
Target.
We aim to develop a concept and a prototype for an application or chatbot that uses AI technologies to support the creation of work instructions to ensure standardized and high-quality documentation.
Approach.
- Using LLMs or other AI tools to help formulate and design work instructions
- Exploring the transformation of audio and video recordings into reusable instructions using AI methods
- Consideration of various forms of presentation in order to meet the requirements of different work processes
Distribution of Activities.
50% development and programming, 30% user experience design, 20% AI training and integration
Useful knowledge.
- Basics in AI and machine learning
- Understanding how to create documentation and work instructions
- Experience with AI platforms, ideally Halerium
- Interest in user interface design and user experience
Additional information.
Attendees are invited to familiarise themselves with Halerium in a free remote training session. During the challenge, experts will be available as mentors for work instructions and AI.
Host and Location.
- This use case is hosted by DE software & control GmbH
- Location: DE office
Motivation.
With the omnipresence of the Internet of Things (IoT), we are looking for cost-effective solutions to connect “cheap” mass-produced products. How can we take advantage of smart technologies without equipping every object with expensive electronics and power supplies?
Target.
Development of a mobile application and backend that make it possible to intelligently manage and monitor simple objects in urban areas and in companies without having to contain electronic components themselves.
Approach.
- Implementation of a system for identifying objects using QR codes or NFC tags
- Development of a user interface that allows users to interact with these objects via their smartphone and receive or transmit relevant information
- Design of use cases such as status messages from street lamps, location determination and fill level indicator of glass containers as well as management of company assets
Distribution of Activities.
50% development of the backend and database structure, 30% programming of the mobile application, 20% design and user experience
Useful knowledge.
- Internet of Things (IoT) basics
- Skills in the development of mobile applications (e.g. Android/iOS)
- Understanding backend systems and databases
- Experience with QR code or NFC technologies
- Interest in urban infrastructure and operational asset management
Host and Location.
- This use case is hosted by HAW Landshut
- Location: TZ PULS office (Technologiezentrum für Produktions- und Logistiksysteme)
Motivation.
Modeling for value creation is a time-consuming and cost-intensive process.
Target.
The aim is to advance the automation of this process.
Approach.
- Identification of key activities
- Development of automation concepts
- Integrate data sources
Distribution of Activities.
60% programming, 40% concept development
Useful knowledge.
- Value Stream Mapping
- NodeRED
- Lean Manufacturing
Host and Location.
- This use case is hosted by NTT Data
- Location: BMW Group Plant Dingolfing (BIZ)
Motivation.
In BMW's complex production environment, there is a wide range of standards, regulations, and guidelines. Planning and defining new business processes and project steps that meet all guidelines can be time-consuming and challenging for employees.
Target.
- Development of a prototype and development of a reliable business
- Use case for implementing a Proof-of-Concept in a real environment
Useful knowledge.
- SQL / Python
- 101 LLM
- 101 Azure Machine Learning
- 101 Azure OpenAI/Azure AI Studio
- 101 Azure Web Apps
Host and Location.
- This use case is hosted by Microsoft
- Location: BMW Group Plant Dingolfing (BIZ)
Motivation.
We use social media to communicate with the whole world. However, the exchange of views in the region is just as important in order to be able to jointly address and exploit challenges and opportunities. A strong democracy and entrepreneurship depend on intensive discussions and networking with like-minded people.
Target.
The aim is to develop an app using the Microsoft Github Copilot that brings people in the region together again and actively promotes the exchange of views.
Approach.
- Design and program an app that allows you to receive and send messages using only specific areas on a map using geotagging
- The freely definable areas can be viewed on a public map and could be described by subject areas in order to be able to exchange ideas with others in a targeted manner
Topics could include:
- What do you think of a bike path in our region?
- Does anyone have experience in 3D printing?
- What ideas would you have for challenge XY in our region?
Distribution of Activities.
50% conceptual design, 50% programming
Useful knowledge.
- JavaScript, Node JS
- Frontend development
- Github Copilot
Target group.
- Programmers
- Psychology students
- UX designer
Host and Location.
- This use case is hosted by Kinexon
- Location: BMW Group Plant Dingolfing (BIZ)
Motivation.
As a plant manager I would like to have full transparency about all moving shopfoor assets in real time to efficiently manage process flows.
Target.
Equipe physical shopfloor assets with KINEXON Mesh sensors to track their position precisely in real time to derive efficient process flows and reduce search times.
Approach.
- Build a digital twin including all physical shopfloor assets in KINEXON OS
- Configure and optimize shopfloor layouts, process flows same as business events with a low-code/no-code interface
- Derive data-driven improvements based on KINEXON Process Mining
- Customize a mobile user interface for three different shopfloor personas applying KINEXON Search&Find
Distribution of Activities.
40% configuration, 30% management, 20% conceptual design, 10% programming
Useful knowledge.
- IoT
- Real-Time Locating Systems
- Process Modelling
- Process Mining
- Business/Management
Host and Location.
- This use case is hosted by BMW
- Location: BMW Group Plant Dingolfing (BIZ)
Motivation.
In the production environment, the identification of changes in production buildings and areas, which may lead to disruptions and production failures, plays an important role. The use of drones opens up new opportunities for regular inspection in terms of speed and precision when collecting the necessary data. Data can also be collected in hard to reach areas of the building infrastructure.
Target.
What is important to us about this use case is the use of drones that are as cheap and commonly available on the market as well as the implementation with open-source AI solutions. The priority is the evaluation of photos and video material. As a result, the user is expected to know where something has changed on the factory premises or at which production building, together with the associated image material.
Approach.
- Understand the data provided, the function of drones and the processing of image and video material, if necessary, depending on coordinates
- Transparency of technical options and solution space
- Development of a solution concept and coordination with users
- Implementation of a software solution
Distribution of Activities.
30% conceptual design, 70% programming
Useful knowledge.
- Programming (Python)
- Image processing
- AI (Yolo)
Target groups.
- IT students
Host and Location.
- This use case is hosted by BMW
- Location: BMW Group Plant Dingolfing (BIZ)
Motivation.
In the painting process, the vehicles go through various process steps from pretreatment, KTL coating, sealing and finally the topcoat. In this process run, the front flap and tailgate must be fixed (pre-treatment) and also opened manually and automatically in the further production steps. The BMW plant in Dingolfing is characterized by the production of a wide variety of vehicle types. The variety of different body shapes, from the BMW 4 Series to the BMW 7 Series, as well as the various drive variants, entail different geometries in the area of the front flap. These geometric differences currently require the use of a wide variety of equipment for the individual vehicle types. This results in high expenditure in the procurement of equipment and subsequent handling during the production process.
Target.
As a result of this task, a design proposal for a standard operating device for fixing the front flap, which can be used on all types of vehicles, is expected. The standard operating equipment significantly reduces the effort required in the painting process.
Approach.
- Understand the data provided (CAD data) and existing bodyshells as well as the use of equipment in production
- Take a look at the installation process of equipment in the paint shop and get an overview of the challenges
- Transparency of technical options and solution space
- Development of a solution concept and coordination with users
- Setting up a demo model with simple means
Distribution of Activities.
30% conceptual design, 30% construction, 30% demo model construction
Useful knowledge.
- Mechanical engineering and construction
Target groups.
- Mechanical engineering
- Industrial engineering
Host and Location.
- This use case is hosted by BMW
- Location: BMW Group Plant Dingolfing (BIZ)
Motivation.
The next generation of batteries is being rolled out at BMW all over the world and is doing so at the same time. With this use case, we want to connect maintenance personnel worldwide and support them with AI when starting up plants.
Target.
The use case is about merging and mapping automatically generated plant data and manually generated maintenance orders using an AI and then making them available for a search in the form of a smartphone app and/or web application.
Approach.
- Dummy data is provided by BMW
- The real data is stored in BMW's CDH (Amazon Cloud Service) must be read from there in the future
- The read data must then be merged and mapped with the help of an AI
- The processed data must be made available to the user in the form of a smartphone app and/or a web application
Distribution of Activities.
50% data modeling with AI, 50% app design (UX/UI)
Useful knowledge.
- Data modeling
- Cloud computing
- AI
- App Design (UX/UI)
- Frontend and backend development
Host and Location.
- This use case is hosted by BMW
- Location: BMW Group Plant Dingolfing (BIZ)
Motivation.
As an assembly planner in a multiproject landscape I want to reduce my manual planning and checking effort when implementing new handling devices.
Target.
Content based summary to get an overview about the status of the implementing process.
Approach.
- Develop a self learning AI module
- Framework and Dataset will be provided
Distribution of Activities.
30% conceptual design, 70% modeling
Useful knowledge.
- Python
- AI
- Cloud-Computing
- Frontend / Backend development
- UX-Design
Host and Location.
- This use case is hosted by BMW
- Location: DE office
Motivation.
The large number of suppliers leads to different types of shipping labels in incoming goods in logistics. The process of manual data reconciliation is error-prone and time-consuming. The employee should be supported by visual data reconciliation.
Target.
The incoming shipping labels from our suppliers should be compared for plausibility with the storage label generated internally by BMW on the basis of 3 important values:
- Delivery note number
- Item number
- Number of pieces
Approach.
- Based on the optical features, these should be compared with the 3 important values
- Various labels from our suppliers and the BMW storage label are provided
Distribution of Activities.
50% development and programming, 30% user experience design, 20% AI training and integration
Useful knowledge.
- Basics of IT and image recognition
- Understanding the interrelationships of logistics
- Interest in user interface design and user experience
AGENDA.
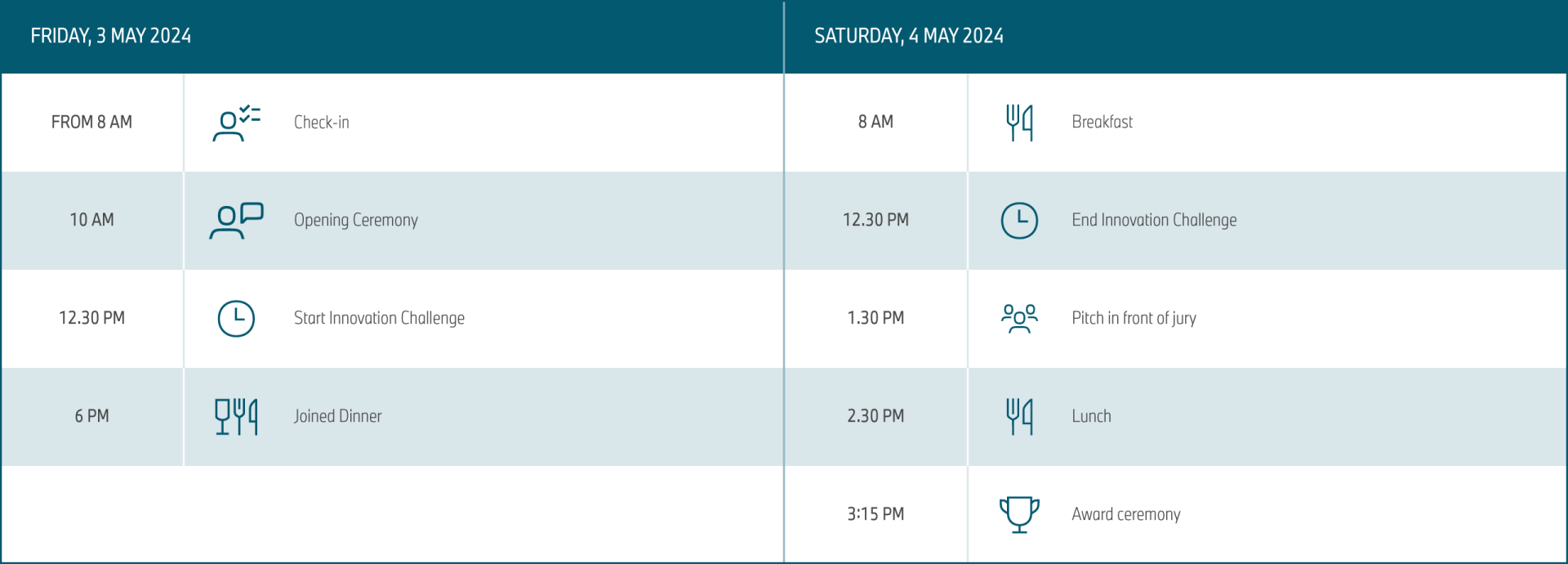
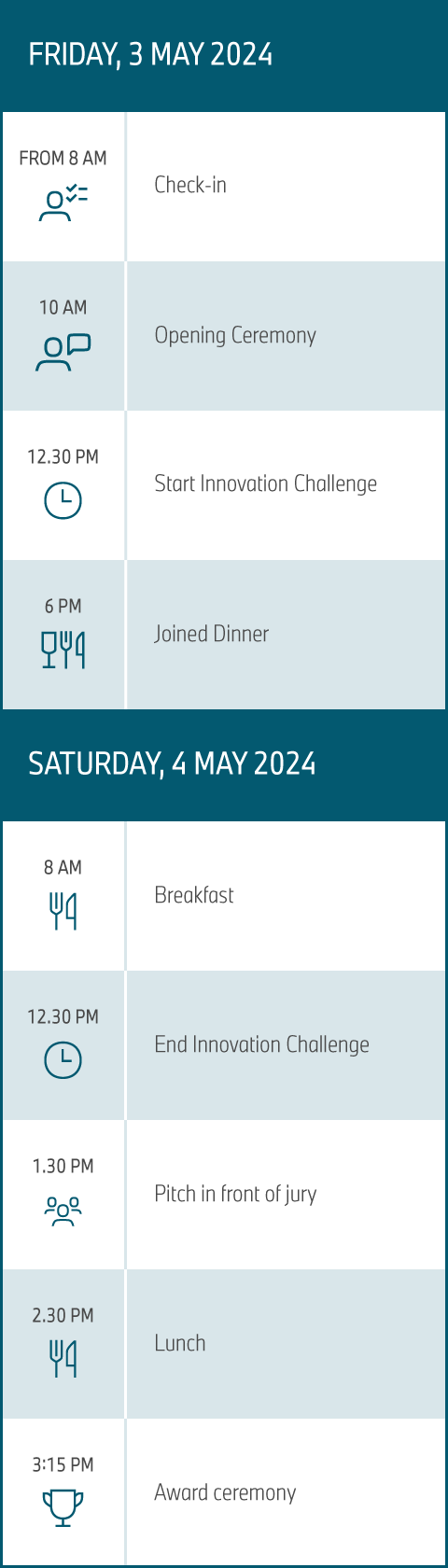
Our cooperation partners.
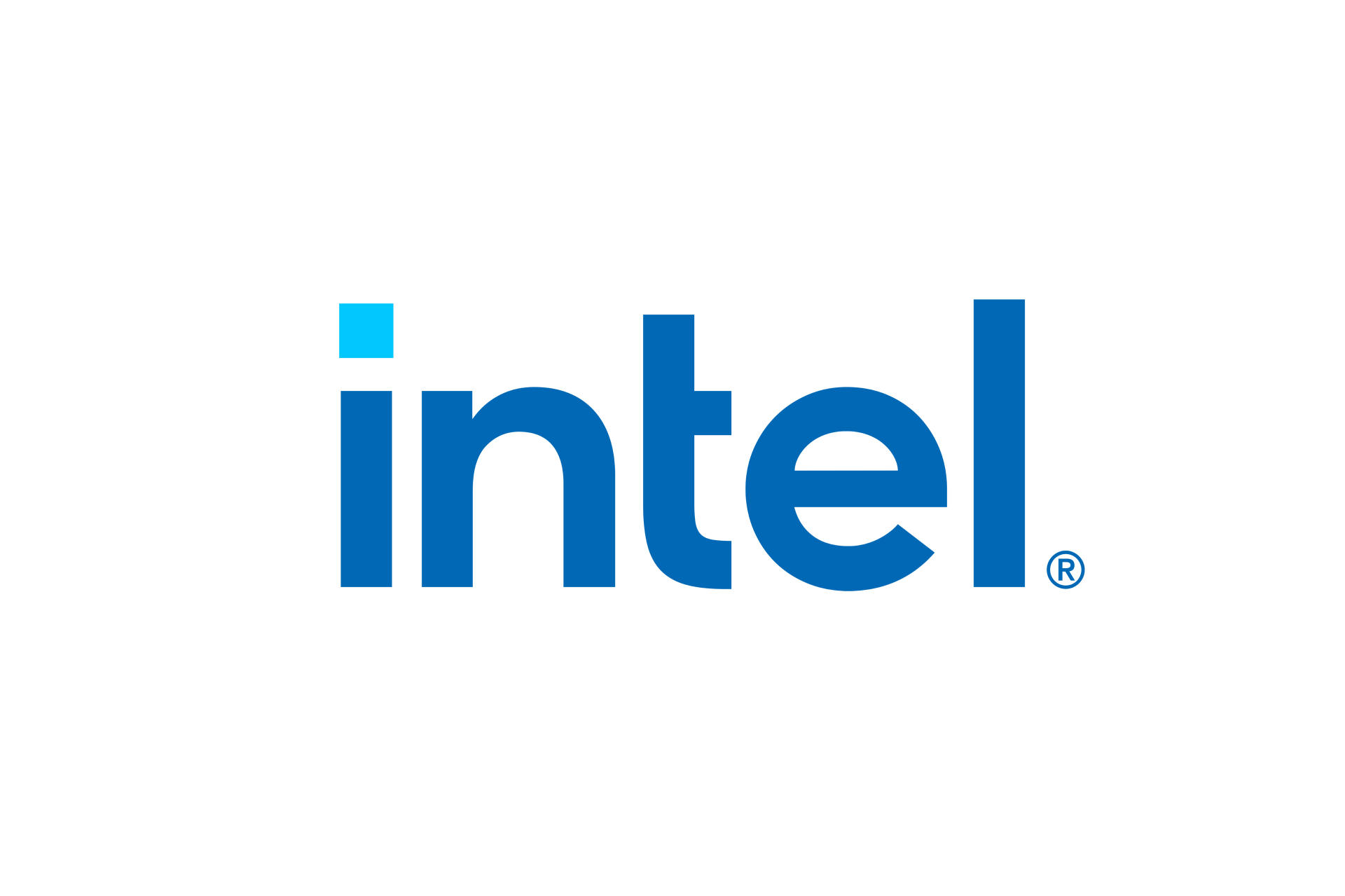
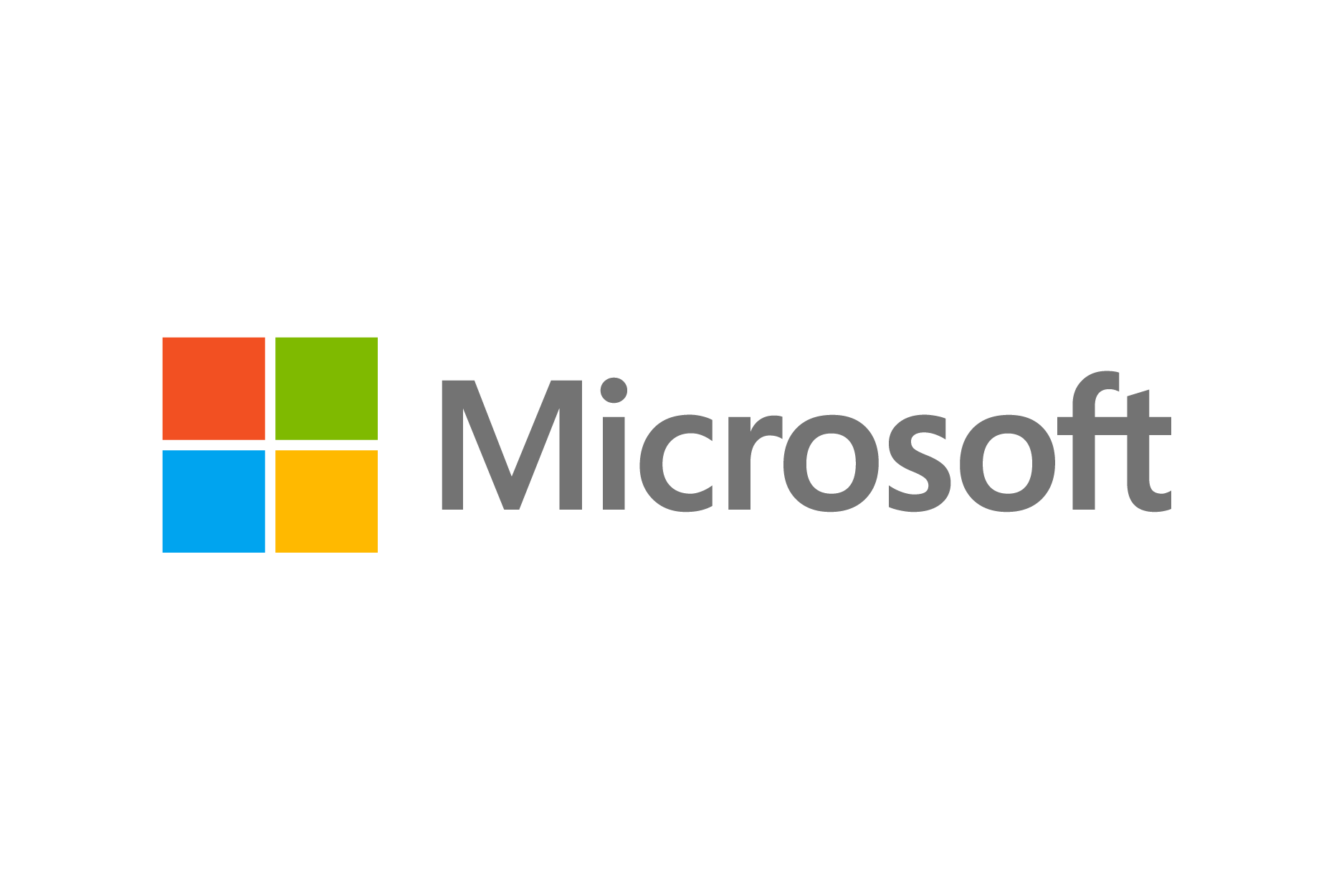
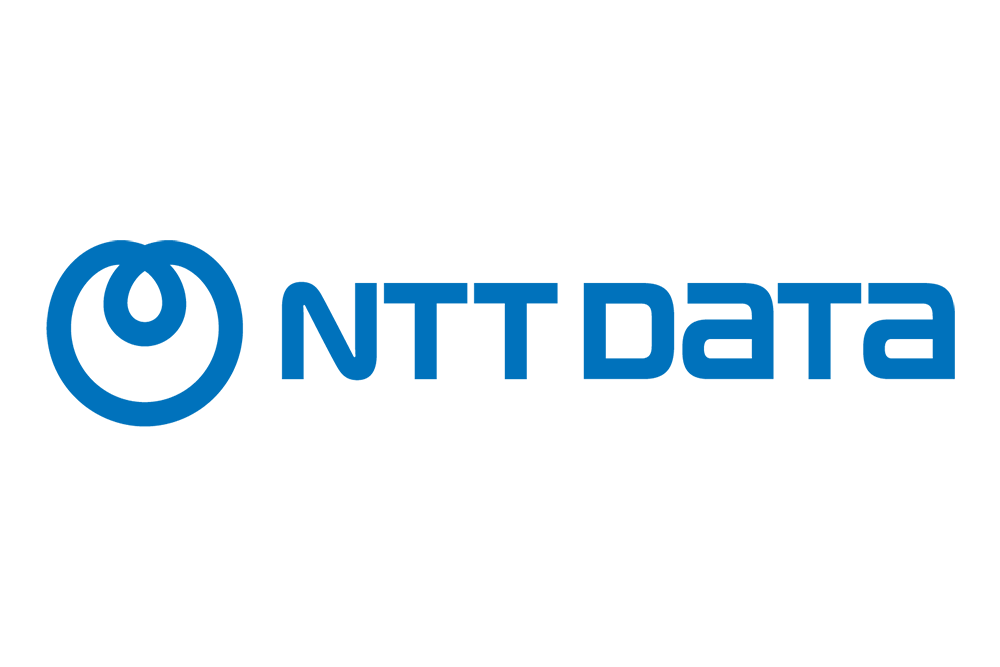
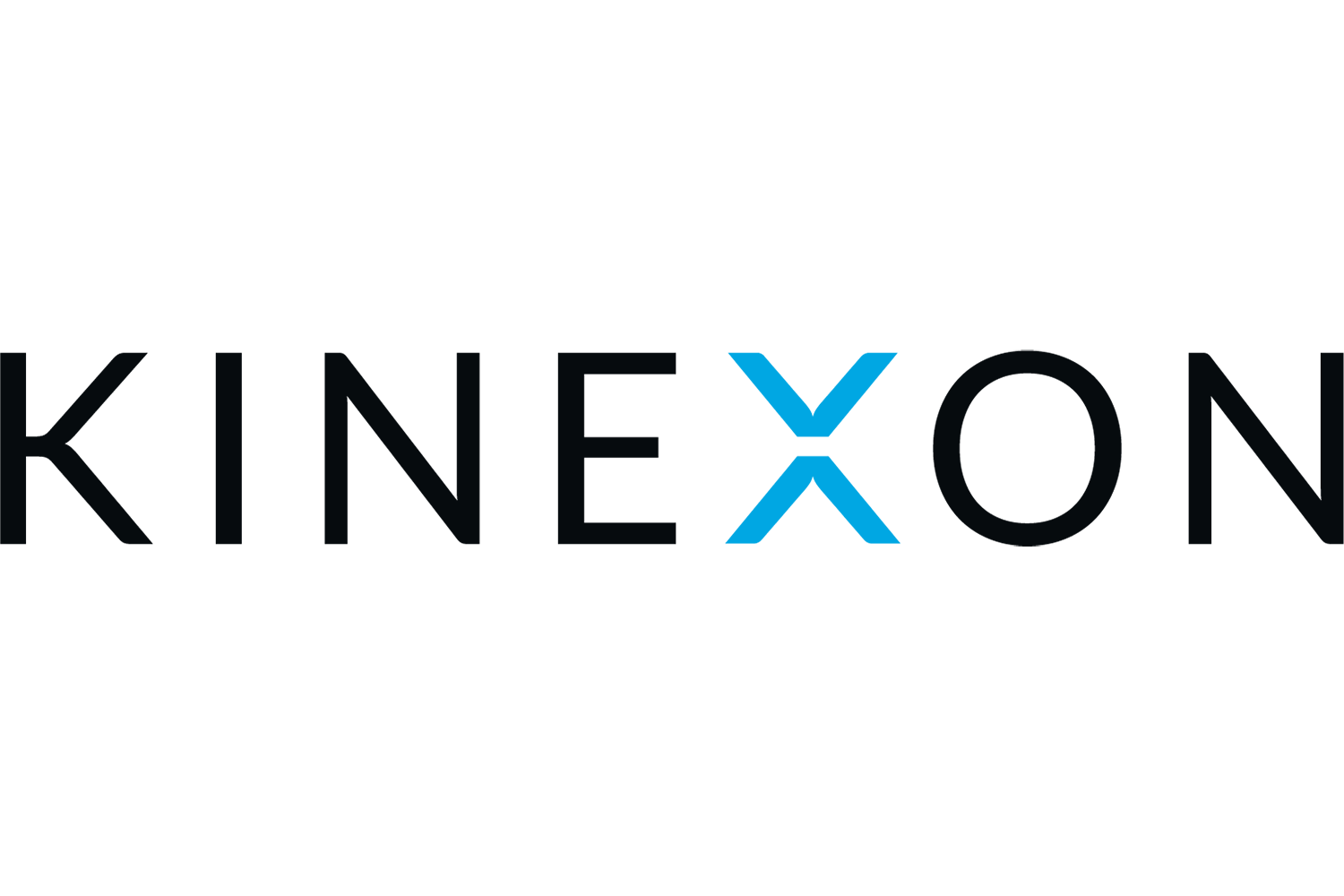
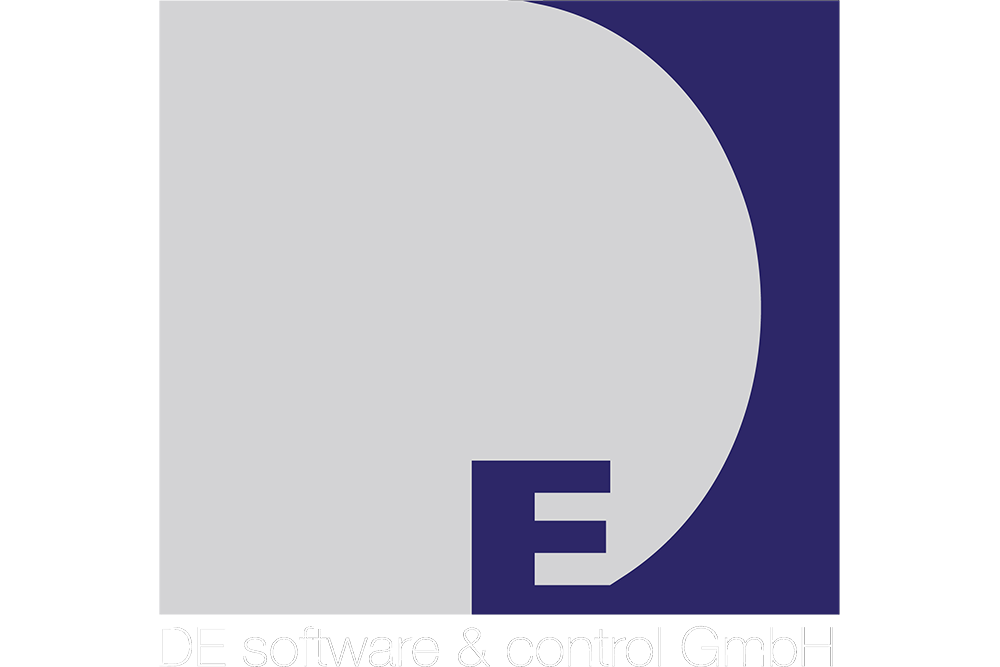
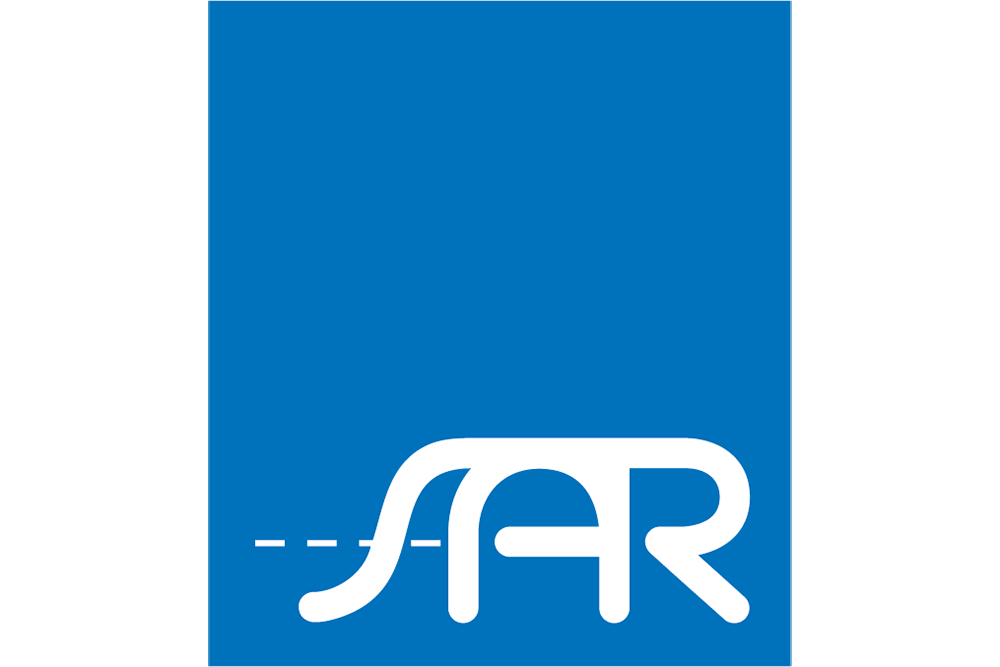
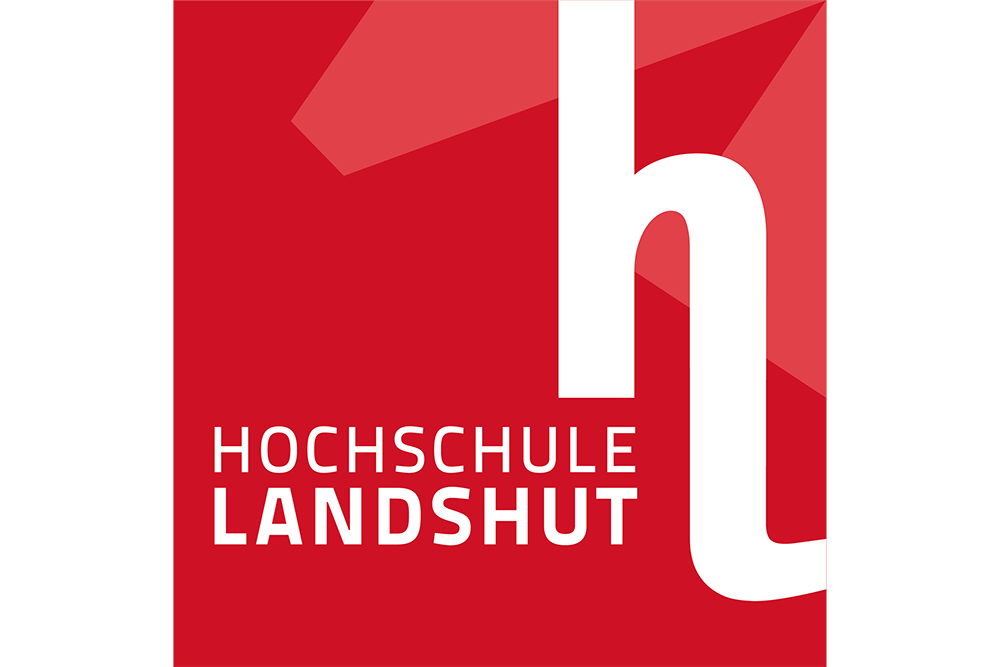
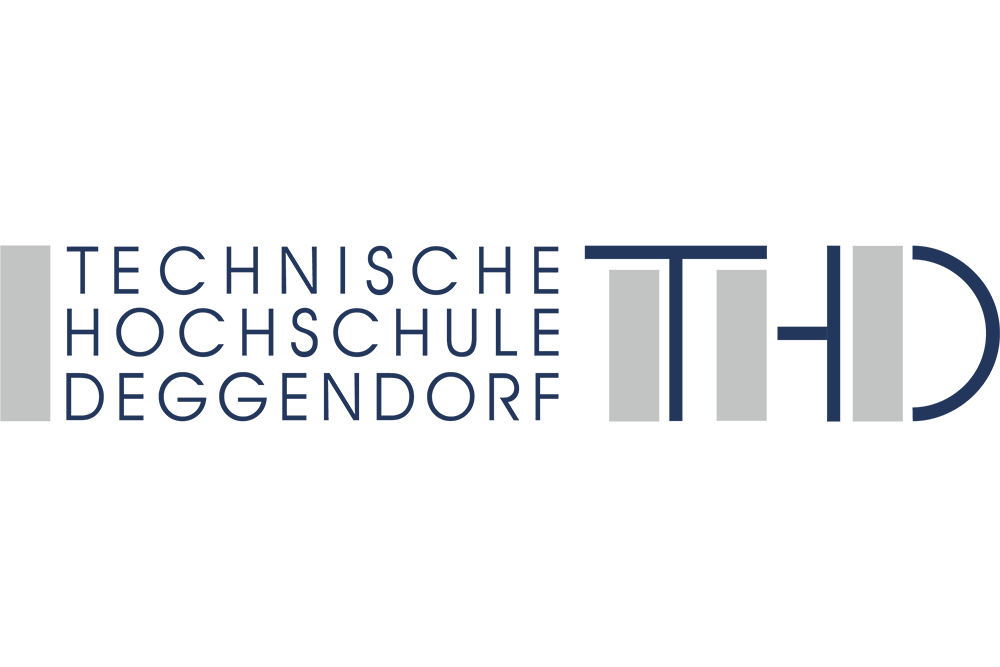